自运行以来,因为种种原因,协调没有投入。运行中发现,火电厂主汽温度自动调节非常困难。波动大,易受干扰。在负荷大幅度快速波动时候,主汽压力不易稳定。当燃料量波动的时候,主汽温度波动也很大。为此,我们进行了多次努力,主汽温度自动调节越来越稳定,最终满足了生产要求。现将火电厂主汽温度控制系统投自动步骤跟大家作以下介绍,也许会有一些启示。
为了行文的简洁,咱们对几个重要参数用符号做个规定:
1、主PID的比例带:δ1
2、主PID的积分时间:Ti1
3、副PID的比例带:δ2
4、副PID的积分时间:Ti2
5、主PID的输入偏差△1
6、副PID的输入偏差△2
7、微分增益:KD 8、微分时间:KT
1、第一阶段 串级调节系统
起初我们设计的时串级调节系统。其控制编程示意图如下:
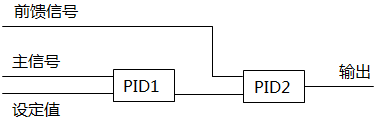
图1 串级控制系统
在调试期间,调试所的人员根据以往的经验,用常规的参数。使用参数大致如下:δ1=100,Ti1=150,δ2=60,Ti2=260。
在PID整定参数的过程中,调试人员,在这个基础上,大约上下浮动50%的幅度,始终不能使得系统稳定下来。系统一直处于大幅度震荡过程。
后来我考虑到我们公司的减温系统可能有其特殊性。经过仔细观察该系统,发现超前信号始终不能发挥超前作用。是不是超前信号采样不当呢?我们的超前信号跟常规系统一样,也采用的是喷水减温后的温度。经过对超前信号和主信号的观察,发现超前信号还是能够超前地反映主信号波动的趋势的。可以断定,信号采集正确。
为了提高超前信号的作用,我大幅度加强副调的比例作用。最终确定δ2=10左右可以正常发挥超前作用。这时候又发现,虽然超前信号起到了作用,可是主信号还是太强,超前信号发挥的作用很不明显。那么就减弱主信号吧。最终整定主信号δ1=320。
为了消除静差,我们逐渐强积分作用。最终确认Ti1=800。
读者可能会发现这里的积分作用有点弱了。这个数值不是有意为之,是在反复衡量之后才得出的数值。本来拟欲增强积分作用,可是总是发现积分作用盖过了比例作用,对系统调节造成了干扰。增大积分时间之后,发现完全可以消除静差,因而确认了这个参数。究其数值过大,可能属于DCS系统的原因。
在调整副调的积分作用的过程中,发现副调的积分作用始终不利于系统的稳定。为此,我们干脆舍弃积分作用。让Ti2大于等于2000以上。
此时,主汽温度自动调节质量有了明显的好转,系统不再震荡。稳定工况下,系统可以正常运行。主汽温度一般稳定在535±4℃。烟气及燃烧稍有波动,温度波动就较大。抗干扰能力较弱。
此阶段最参数如下:δ1=320,Ti1=800,δ2=10,Ti2=2500
2、第二阶段 导前微分调节系统
总结第一阶段温度波动的原因,发现即使有超前信号作为前馈,但是系统反应还是不够快,再加上执行机构有一定的死区,所以往往等到阀门流量有反应的时候,主汽温度已经开始变化了。经过观察,从超前信号开始变化,到主信号有变化,之间的时间滞后,大约为 30 秒左右。这么短的时间,超前信号所起到的超前作用比较微弱。
为了克服这个问题,能不能使用带有导前微分的自动调节系统呢?我公司的DCS由北京和利时提供,在线修改下装比较难。只有在听炉时候修改下装比较安全。因为修改下装一次比较困难,为了稳妥起见,我设计了个带有导前微分功能的串级调节系统。在必要的时候,在导前微分模式和串级模式之间可以互相切换。
具体编程如下:
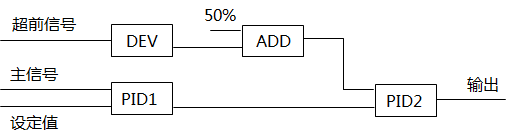
图2 带导前微分功能的串级控制系统
在上图中,微分块和PID2模块之间,增加了一个加法模块。因为超前信号经过微分之后的数值,始终围绕在0左右波动。为了观察方便,特在微分功能之后加了50%,没有其它额外的作用。当使用串级功能的时候,令微分增益KD=0即可。
经过调试,发现我公司的锅炉,更适用于导前微分调节系统。
在导前信号一有波动的苗头,微分作用马上使阀门开度变化。在波动来临的时候,微分作用可以根据变化速率使输出比串级系统更加快速调节。更重要的是微分作用的另一个特性:波动来临时,微分增益使得输出变化,波动停止的时候,即使这个波动没有向相反方向回调,而保持在静止状态,微分作用也会因为自身的原因,使得输出开始回调,因而更显得“导前”信号的超前调节作用。这个“超前调节”带来的超前作用,往往比超前信号更要超前。我们知道:超前信号在波动结束的时候,往往会有个相对静止的平稳期,然后再向相反方向波动。因而,微分时间带来的超前回调作用,显得非常重要了。
那么,我们需要注意的就是,因为微分增益的原因,可能会给系统输出带来微小而快速的抖动,造成执行机构反复动作。增加微分时间,可以消除抖动。可是增加了微分时间,有可能会使超前作用减弱。要消除抖动和超前之间的矛盾,需要对微分增益和微分时间作个比较合适的考虑。
最终,我们得到如下的调节参数:δ1=160,Ti1=255,δ2=20,Ti2=2500,KD=55,KT=55。
根据系统的不同,上面这个参数也会有改变。我们同一台锅炉,两套主汽温之间的参数就很不一样。另一套参数如下:δ1=255,Ti1=255,δ2=4,Ti2=2500,KD=15,KT=75。
因而,提醒读者注意:本文所提到的参数仅作参考。本文得出的主要经验就是:不能拘泥于以往的经验对待所有的自动调节系统,而应该根据具体情况,设定合适的参数。不管这个参数跟以往的经验区别再大,只要系统稳定,参数就算合理。
最终得到的调节效果是:稳定工况下,主汽温度维持在535±3℃之内。系统抗干扰能力有了大幅度提高。
主蒸汽温度制动调节效果图,见附图1、附图2。
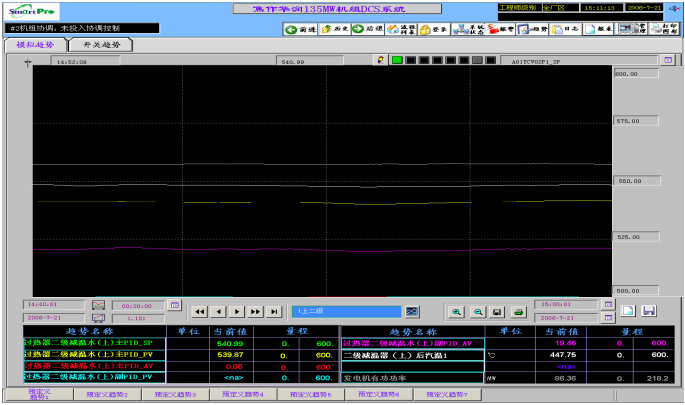
附图1:导前微分调节系统正常工况调节效果图。时间跨度1小时
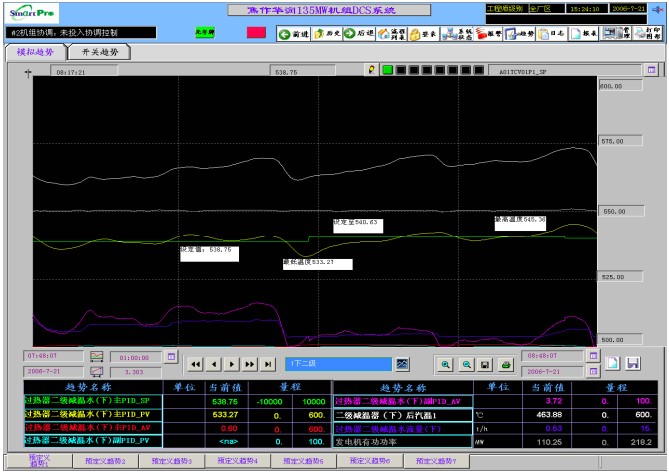
附图2:导前微分扰动工况主汽温度自动调节效果图。时间跨度1小时
3、第三阶段 带有导前微分和减温水负反馈功能的串级调节系统
第二阶段的调节效果虽然有很大效果,但是我还发现了许多不足。总结起来有如下几个方面:
①执行机构动作频繁。执行机构反复开关,虽然动作幅度不大,但是时间久了,可能会对阀门特性曲线不利;
②由于阀门存在一定的空行程,执行机构的动作很多都属于无效调节。一方面造成执行机构徒劳无益的动作。另一方面,空行程也抵消了一部分的超前作用。
空行程几乎是所有自动调节系统都存在的问题,也几乎是不可避免的问题。对于一些不大敏感的系统,这个问题大都可以忽略。但是因为我公司锅炉的抗干扰能力较差,经过仔细研究,在解决了其它问题之后,这个问题就凸显了起来了。
以前我在别的地方曾经尝试用了一些手段来弥补空行程,可是程序较复杂。和利时软件运行后修改程序较为困难。这个方法不能使用。
那么,我考虑到,加入流量反馈,加强积分作用,PID1 的输出去控制减温水流量,只要PID1的输出与减温水流量有偏差,PID2就不停的运算,直到减温水流量变化,达到了PID1的输出的要求为止。经过反复考虑,理论上行得通。关键在于PID2 的积分作用要足够的强,使得PID2的输入端只要有偏差,输出端能够在几秒钟内,不断地依靠积分运算,命令阀门动作,去弥补这个偏差。
具体编程如图3:
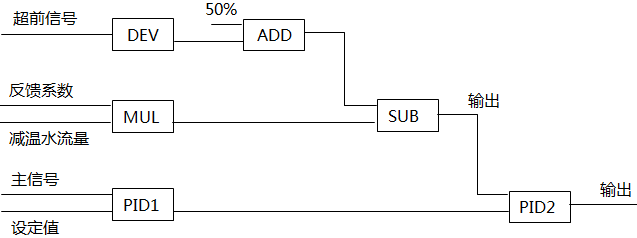
图3 带超前微分和前馈量的串级控制系统
考虑到可能因减温水流量信号过强,造成系统震荡,特给该信号加了一个系数。
编程设计下装后,经过多次PID整定,确认参数如下:δ1=330,Ti1=555,δ2=20,Ti2=5,KD=40,KT=88;流量系数=0.58,PID2的死区=0.07。考虑到超前信号不断的变化,微分作用运算使得PID2的测量值不断地处于波动中,可能会造成执行机构不停动作,电机可能会因过热烧坏。因而给 PID2加了个死区。
经过实践检验,确认这个方案是可行的。主汽温度自动调节系统抗干扰能力也大大加强,即使在负荷有大幅度波动的情况下温度波动范围也不超过±5℃。最终主汽温度的偏差在548±3℃之内。执行机构要么不动作,要么较大幅度动作,彻底克服了执行机构的空行程。在标准工况和一定的干扰工况情况下,一般人工干预往往还不如自动调节效果好。在大扰动情况下,适当修改设定值,可以使得温度仍然波动达到要求。
调节效果图,见附图3和附图4。
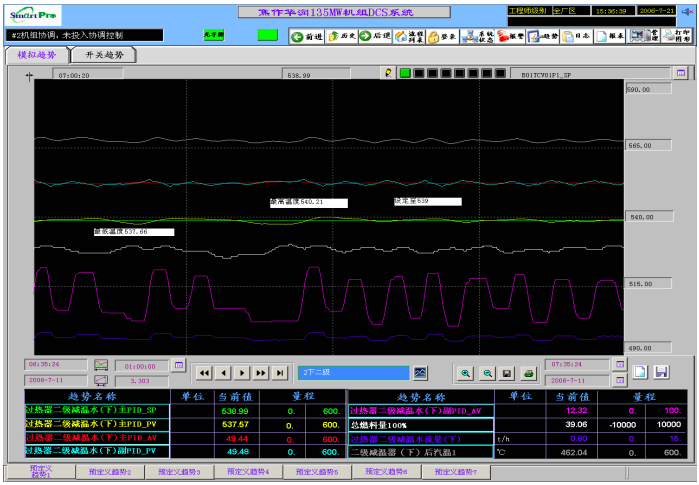
附图3:带反馈调节系统正常工况效果图。可以看出,执行器要么不动,要么动作直到流量有变化才停止。时间跨度1小时。图中,似乎执行器动作很频繁,但是统计1小时内动作次数在25次,不会造成执行器过热的。
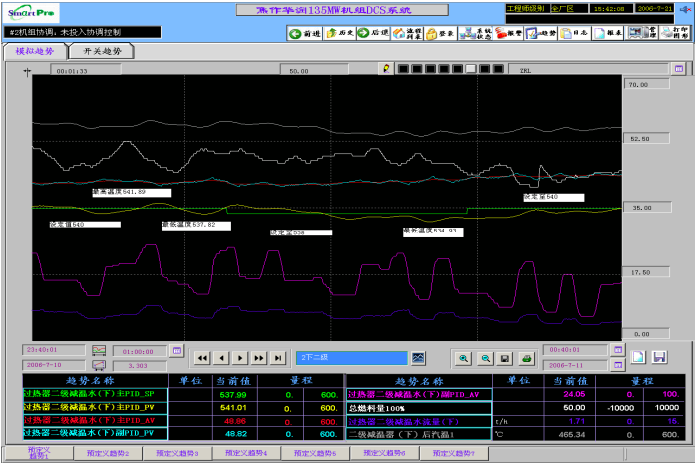
附图4:带反馈调节系统扰动工况效果图
4、今后还可能可以改进的地方
为什么负荷大幅度快速波动的时候,主汽温度会波动较大呢?假如负荷快速升高,我公司的操作人员往往要修改主汽压力定值,欲使主汽压力快速增加,这时候燃料量急剧加大,烟气流速加快。主汽管道吸热面此时会因对流加强,使得主汽温度快速升高。同时,当负荷增加的时候,蒸汽量增加,单位蒸汽吸热量降低,都会导致超前气温会急剧增加,减温水即使急速增加,往往还是有点慢。造成温度过高。如果我们使得主汽温度自动调节系统运算加强,又可能造成稳定工况下系统震荡。
怎样才可以弥补因为烟气流动和蒸汽量波动带来的温度波动呢?我初步考虑,需要再增加一个总燃料量信号。经观察,从总燃料量开始波动,到主汽温度有反应,大约有1分钟左右的间隔。这样燃料量波动带来的减温水调节可能过于“超前”,因而可能调节质量反而下降。为了消除这个问题,需要在总燃料量后加一个纯滞后功能。然后在调试过程中,多次调节纯滞后时间,应该可以达到要求。这个思路没有经过验证,不知道能不能行得通。也许真正实用的时候,要经过许多修改和探索吧。
5、需要说明的问题
各个电厂的环境工况设备不同,PID参数设置各有不同。不可拘泥某个经验参数。在上述主汽温度自动调节系统调试过程中,所列举的参数,仅可以作为参考。附图中,调节效果完全有可能会再进一步提高。同时,如果协调投入自动,温度控制会可能再上一个台阶。本文目的在于阐述作者自己的整定参数的思路。我的思路也有盲区,欢迎各位批评指正。
作者:白志刚(河南焦作华润热电有限公司技术部)
相关阅读
火电厂自动调节系统和调节系统考核参数
浅析火电厂中间仓储锅炉主蒸汽温度控制的若干问题
电厂汽机主汽温度比锅炉主汽温度高的原因和处理方法